Scandinavian Homes pioneered energy-efficient houses three decades ago. There might be more were it not for the planners, writes Kathleen O’Callaghan
Energy efficient houses are all the rage now, and Lars and Linda Pettersson were way ahead of their time when they set up Scandinavian Homes in Galway in 1991.
This specialist in ‘passive houses’ has modest annual output, but the business has provided a nice lifestyle for its owners.
Lars Pettersson is from Lysekil in Sweden, and his wife and business partner, Linda Kelly, hails from Moycullen in Galway. After they met, the couple lived in a cosy timber house in Lars’ hometown. Linda’s mother, a frequent visitor, fell in love with her son-in-law’s house and asked him to build a similar abode back in Moycullen.
“Lars put his mind to building a low energy home for mum, and from that initial build we set up a company to construct similar homes in Ireland,” Linda recalls.
“Lars researched the technical data to meet the certification rules. We were initially thinking of setting up the factory to make the houses in Ireland, but it was easier to establish the factory in Lysekil.”
With a plentiful supply of timber and experienced craftsmen in Sweden, the venture manufactures house components such as wooden beams, wall panels and felted roof at Lysekil and then ships the parts over to the west of Ireland for assembly.
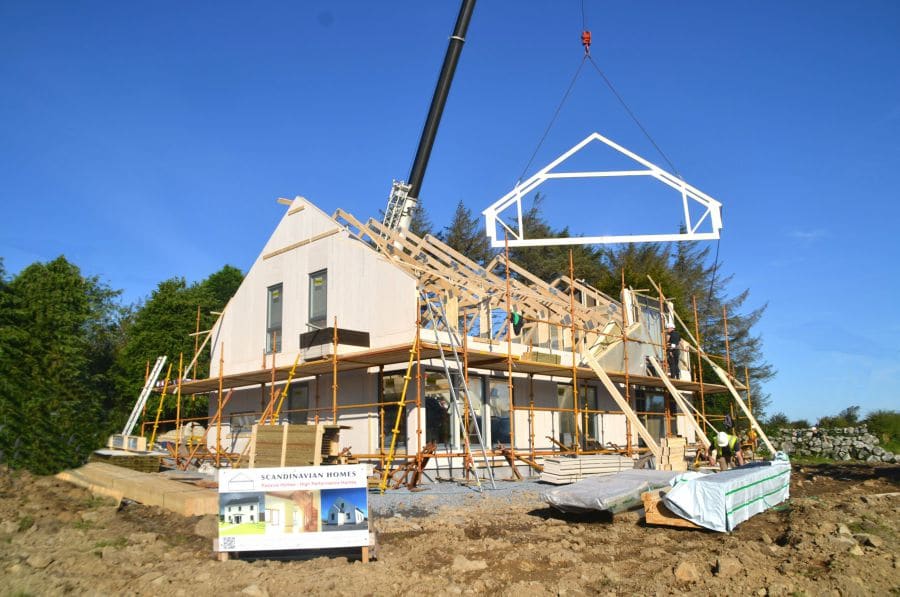
A Passive House (Passivhaus in German) is designed to require minimum energy in order to stay at a comfortable temperature during winter and summer.
They originated in 1988 as a collaboration between Bo Adamson from Swedish University Lund, and Wolfgang Feist from the German Institute for Housing and the Environment.
The thermally efficient building aims to maintain an indoor temperature 20°C year-round, with space heating required for two of the months of the year.
Most Passive House buildings use heat recovery systems via internal ducts. Natural light is maximised with large south-facing windows, and solar heating is also key to the concept.
In order to reduce heat loss in winter and heat gain in summer, windows are triple glazed, special coatings between the panes to create heat and avoid condensation. Walls are insulated with cellulose made from recycled newspaper.
The cost of a Passive House isn’t strictly related to the size of the build. Excluding land cost, a 2,000 sq. ft house has a price tag of c.€230,000, while a 1,000 sq. foot house comes it at c.€175,000.
If constructing the houses is not overly complex, negotiating red tape is trickier. The Petterssons had to adapt to a raft of building regulations introduced in the mid-1990s. “There are odd rules, such as you must have a water tank in the attic,” Lars explains.
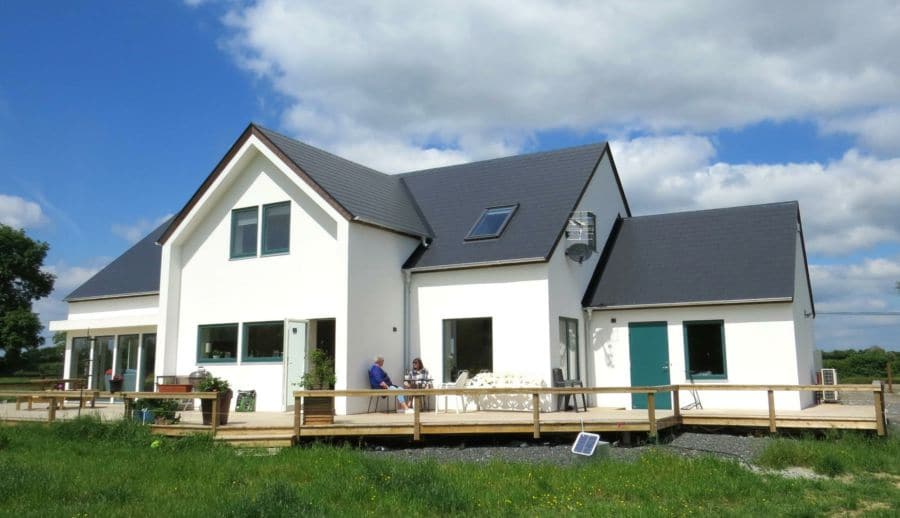
“Then some local planners didn’t want our houses to have a timber exterior finish in certain settings. They wanted them to look like the houses nearby, and we solved that problem by cladding the timber with cement panels.”
Securing planning permission for one-off housing, no matter how sustainable, has become an increasing challenge in Ireland, especially in under-populated western counties.
“It’s very hard on young couples who are trying to build on their own site, often on land owned by their parents,” says Linda. “Many couples want to build close to their parents’ home but can’t get the permission. Maybe it’s a kickback reaction to the days of bungalow blitz and ribbon housing.
“If you want to build this side of Galway, you have to have grown up here. Nobody likes these rules. Most of our customers are young couples who are building their first family home. There are also older couples who are downsizing in order to hand over the homestead to their children.”
When planning permission is granted, assembly of the Scandinavian Homes’ modular builds is rapid. According to Nils Pettersson, the couple’s son and a recent engineering graduate: “The average house takes only about two weeks to produce in the factory. When the component parts are ready, it is shipped to Ireland for assembly. Once the parts arrive at the destination, it will take four to five days to erect the building.
“Once the house is constructed, then it’s time to fill the cavities and insulate the building. Customers can have the structure fully fitted out with kitchen cabinets, utility area and bathroom units if they wish. In a short space of time, you have a beautiful long-life home working on the lowest energy principles.”
Lars Pettersson (65) remarks: “With our houses, the owners can see what exactly is going into their homes every step of the way. When you look at the problems facing thousands of homeowners with mica and pyrite, you would wonder how those defective buildings passed all the building regulations and were given insurance certs as well.”
The family, based in Moycullen, has built 350 houses since its inception. Current output is 15 to 20 houses a year, though the Petterssons intend to slowly expand at a steady pace on an annual basis. There is scope to do so: their operating company had a net worth of €3.4m in December 2020, including €1.5m in cash.
The Petterssons have reared their three children in Moycullen. Daughter Linnea works in Sweden and their other son Eric is in college. As Nils immerses himself in the business, the founders are branching out. “We are starting up another venture growing organic Irish hazelnuts and creating our own orchards,” says Lars.