Trifol Resources was this week awarded €3m in funding from the EU to scale its PLASTIC2WAXLIFE project, which turns waste plastic into sustainable was via a process of thermal conversion.
Founded by waste management industry veteran Pat Alley, Trifol has invested €7m since 2015 to develop its patented products and processes, validating its scalable thermal conversion process known as modular pyrolysis at Queen's University Belfast and piloting the plant technology in Portlaoise.
Pyrolysis refers to the thermal composition of materials in a vacuum. The plastic is heated up 500°C in an inert environment -- so no flames, no oxygen and no emissions -- converting the plastic into a gas vapour.
When the gas is chilled it becomes wax and residual fuel byproduct, and with as much as 400m tonnes of plastic produced annually, only 16% of which is recovered, and the primacy of the corporate social responsibility agenda, there is a potentially huge untapped market for Trifol's services.
"We would have a very high yield of wax, we would try to optimise the production of wax. Why? Because the wax industry and the wax price is decoupled from the dollar price on the barrel of oil," Alley says.
"The price of wax has been pretty stable at about$1,000 a tonne, and with Covid and when the Ukraine crisis came it has now increased to around $1,500, and $3,000 per tonne for the highest grade."
"We have large corporates who yearn for our technology because we can lift the plastics that they recover and give them an independent certification that the plastic was destructed by us and produced the following products that were sold into an industry that of value like wax oil, for example into the cosmetic industry, or low-grades of wax would go into tyre production."
Following a €5m cash injection, 60% of which is coming from the EU LIFE programme for climate action technology, the company will begin the process of ramping up operations, scaling from processing up to 24,000 tonnes of plastic per year at its Bord Na Móna-owned facility in Littleton, Co. Tipperary.
Alley himself started his career as an accountant and helped to integrate and standardise the systems of the 25 cooperatives that would form Irish dairy giant Avonmore, latterly Glanbia.
He rose to the role of head of fresh products and was the youngest member of the company's executive board before, as he put its, growing "restless" after 16 years and leaving to join IAWS, now known as Aryzta, and then becoming CEO of Monaghan Mushrooms.
Alley then spent several years around the millennium in consultancy, learning the food and drinks business, the lingerie business and the waste business before founding AES in 2001, sensing an opportunity at a time when the waste management in Ireland was "immature and developing".
After working with Societe Generale's Vivendi for six months, he decided to buy the Irish franchise for the firm's technologies. However, back home none of the major companies in the sector had any interest in buying the technology as Ireland was in a "non-conforming regulatory period" and content to stick with its established practices.
"Technologies did not matter to the waste industry, so what I did is by going around and knocking on the doors of all the waste operators, I got to know and like some of them an awful lot so I decided to go after raw material," he said
"I drew up my business plan and on a blank page started what the Americans call a roll-up, and I went in and acquired 15 family businesses over a period of about three years."
Having projected earnings of €7m after three of four years, AES achieved that revenue target within six months.
Ultimately, Alley and his advisors built a business that managed 500,000 tonnes of municipal solid waste with a turnover of €60m and a number of materials recovery facilities, making AES one of the leading companies in the industry behind Greenstar.
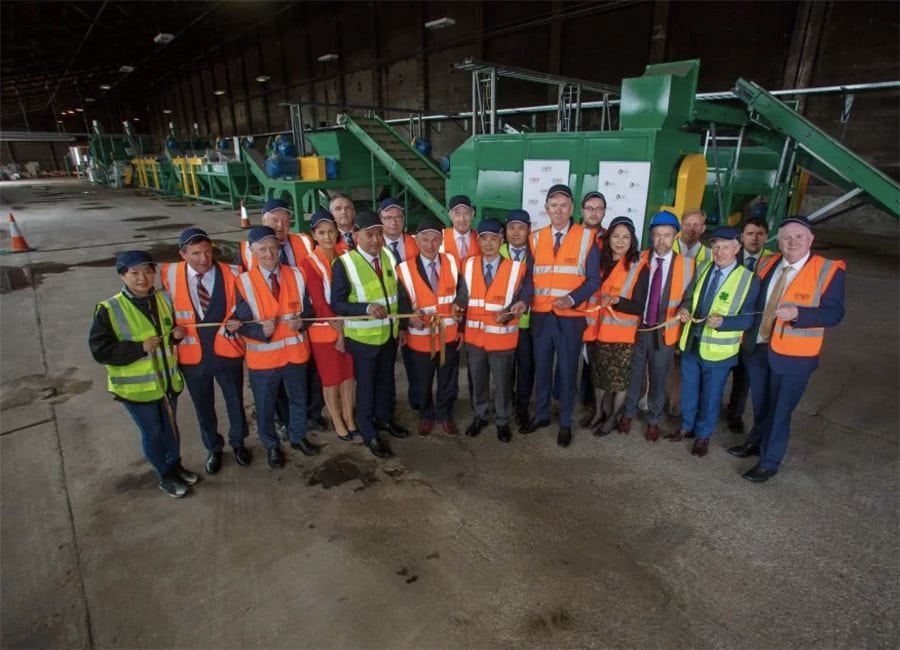
Bord Na Móna came calling in 2007, needing waste to fill a state-of-the-art landfill in Co Offaly that the state agency mistakenly believed the waste industry would rush to use, acquiring AES for around €63m.
"They made a strategic decision, Bord Na Móna, to acquire my business. They were looking for a compliant difference because I found that my biggest unseen cost was the cost of bringing non-compliant businesses into compliance, so we prided ourselves on doing that at an extraordinary cost."
In addition to getting to grips with the waste management business' various strands and factions, Alley learned how much waste ends up either incinerated or in landfill and the financial and environmental benefits of recovery.
Alley's final stepping stone before Trifol was Cynar, a Laois-based company that converted waste plastics into fuel before entering into liquidation in 2015 when oil prices crashed from $100 to $30 per barrel.
Alley rued his decision to invest in a franchise from Cynar when the market sank, but aligned himself with former BP scientist Dr Martin Atkins of Queen's University, who was researching added-value byproducts from oil such as lubricants, plastic and wax.
"About 4m tonnes [of wax] comes out of a byproduct that comes out of an oil refinery, and I saw that wasn't a single product. I saw it as a multi-product and therefore relatively derisked in terms of product multiplicity and end uses.
"I invested about €500,000 in a pilot plant that was established in Queen's University, and through the trialling and production in R&D, we filed for four patents, two for products and two for processes, in the UK, the US and the EU. After many years, we have been granted patents by all those offices.
"When we finished that work in 2017-18, I then set about trying to buy the plant assets in Cynar out of liquidation, which we successfully completed after three years."
Trifol is now leasing a Bord Na Móna facility that it will modify and enhance as required before commencing production on phase one later this year, with production set to increase to 24,000 tonnes when a new plant is completed as part of phase two next year.
Alleys says customers in wax are very few, but it is a lucrative business as wax has applications across food grade, cosmetic grade and medical grade classes. Trifol has developed close relationships with the likes of German oil refinery H&R, which will acquire all the plastic and wax produced by Trifol.
Phase three will see the company engage with a number of family-run waste management operators in the London market that previously exported waste plastics to China, and are in need of a new solution provider for their plastics. Trifol also plans to create a centre of excellence to train Irish graduates across engineering, chemistry, quality control, sales, marketing and accounting.
"We have a big task in front of us - a very exciting one, a very challenging one," Alleys says. "Out of Littleton, when we have a small commercial plant of 4,000 tonnes and a 24,000 tonne plant, we will then have a benchmark plan that can enable global outreach.
"We can sell licences of the technology. We can do joint ventures, where we would be the junior partner and then sell plants, sell the design and the whole lot, turnkey operation.
"People are knocking on our door on a consistent basis, yearning for the technology that we have. We have to crawl before we walk and be very serious about the way we build our business, building slowly on the blocks that we know will stand up.
"The grant has given us an enormous boost in terms of money, and confidence. To get that level of support from the European Commission and from the Irish government is quite staggering."
Photo (l-r): Pat Alley; David Bradshaw, H&R UK and Benelux; Ulrike Volrath, H&R Germany; Alistair Wilding, H&R UK and Benelux; and Dr Thorsten Frick, H&R Germany.