In July 2020, the BMW Group set itself a new, ambitious goal to reduce CO2 emissions by 2030 with goals that cover the entire life cycle of its cars and motorcycles, from the supply chain through production to the end of the use phase.
The aim is to significantly reduce the CO2 footprint of all aspects of BMW’s business and take its place in the circular economy, because the fight against climate change and the way we use resources will determine the future of our society – and that of the BMW Group.
However, what really matters is that we make an effective contribution to environmental and climate protection here and now. To implement concrete measures today and transform the framework for personal mobility for future generations, a strong and passionate team is the foundation. This is based on the underlying guiding principle that sustainability can only be progressed with a workforce that takes responsibility.
Sustainability is not just a trend at BMW. The company have been taking responsibility for 50 years, when the first Environmental Manager in the automotive industry was appointed in 1973. BMW was the first automotive manufacturer to produce a Sustainability Report in 2001. Since 2020, the BMW Group only uses renewable energy sources, and 99% of the annual production waste is recycled.
Specifically, the BMW Group aims to cut CO2 emissions from the entire vehicle lifecycle of the car by a minimum of 40% by 2030. To detail this, the lifecycle is broken down into three distinct stages: the supply chain with suppliers and companies it works with; the vehicle production phase; and the use phase, when customers are driving BMW and MINI cars and motorcycles.
Supply Chain
The BMW Group is taking a pioneering role to set concrete CO2 targets for its entire supply chain and will reduce CO2 emissions in this area by 20% by 2030. For example, since 2020 cobalt and lithium purchased for battery cells is sourced from certified mines in Australia and Morocco. At BMW’s factories, biodiversity is also promoted through ecological habitats. There’s even a real buzz above the parent plant’s roofs in Munich where 160,000 bees call home. These habitats help pollinate green areas in and around the home of BMW. This work is thanks to several voluntary beekeepers who have day jobs at the Munich plant and have made beekeeping their hobby. Almost all BMW’s German plants now support bee colonies, and this is just one small example of how sustainable practices are being incorporated to every part of the business.
Production Phase
A target of an 80% reduction of CO2 emissions by 2030 has been set, committing to the lowest possible level of resource consumption in production of BMW’s cars and motorcycles. This will be achieved in part by re-using materials in the manufacturing process.
At present there is an average of 30% of re-used or ‘secondary materials’ contained within each car that BMW builds. This will increase to 50% by 2030, with these secondary materials coming from vehicles that have reached the end of their useful life and by-products from elsewhere within BMW's manufacturing processes. Factories are also assessed for the optimum efficiency, and since 2020 all of BMW's external power supplies have come from renewable sources, making BMW the benchmark for other manufacturers. This includes a wind farm at BMW's plant in Leipzig, and hydroelectric supplies for its Munich and Dingolfing factories too.
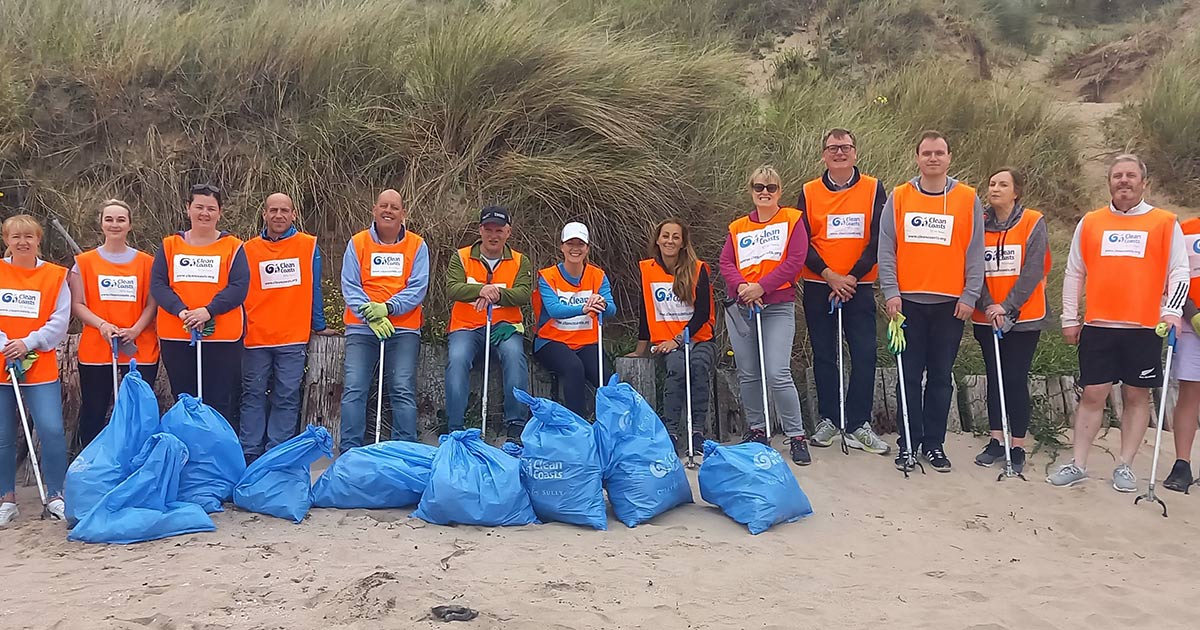
Use Phase
BMW Group is aiming to deliver 10 million fully electric vehicles over the next decade with sustainability at their core. This year BMW Group will have 15 fully electric models in production include the iX SAV, i4 Gran Coupé, iX3 SUV and the all-new BMW iX1 and i7 models launching later this year. The MINI brand will have an all-electric product portfolio from the early 2030s.
At the end of a car's useful life, BMW is reducing it back to its raw materials for use in the manufacturing process. This is just one way to increase the use of secondary materials in a car's construction, while future products will be designed and engineered to accept these materials. In fact, BMW can already re-use up to 90% of the material found in its high-voltage batteries.
BMW also recognises the importance of social sustainability with its workforce, partner suppliers and society in general. For employees, that means career development and talent management, as well as promoting staff diversity across the company in a working environment that encourages personal growth.